DSPORT Issue #254
By Michael Ferrara // Images by Jun Chen
Why copper? With the increasing availability of high-performance, multi-layer-steel (MLS) head gaskets, one might question why anyone would want to use something different. While MLS head gaskets might make sense on the majority of high-performance engine builds, copper head gaskets still have a place. Today, many Top Fuel engines and many Pro-Mod nitrous- oxide engines use copper head gaskets. Copper head gaskets can also be a good choice for a street-performance vehicle. As with any performance part, a thorough understanding of the technology is a must.
Composite Head Gaskets
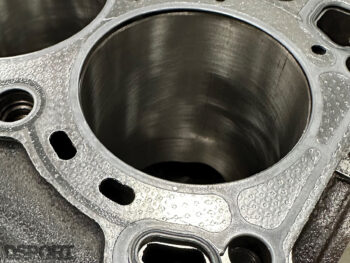
MLS Head Gaskets
Today, the majority of modern engines use an MLS head gasket. An MLS head gasket has advantages over a composite head gasket. First, an MLS head gasket can have a significantly longer service life. Since the gasket is made of steel and not a sandwich of fibers and particles, it tends to su er less material break down. Second, MLS head gaskets provide superior combustion ring sealing. Since the folded, embossed or stopper layer is integral with the metal layer, the combustion sealing ring stays in place better than a composite head gasket. However, the quality of the sealing varies amongst different manufacturers and designs of MLS gaskets. Not all MLS gaskets are created equal. The high-quality ones will perform miracles and the cheap ones will cause headaches. While offering advantages over composite head gaskets, all MLS gaskets require a smoother surface finish (Ra <30 or better) to deliver a proper seal. While OEM engine manufacturers can establish these smooth finishes on the engine production line, many machine shops lack the proper equipment to replicate this smooth finish. When an MLS gasket is used with a finish on the block or head that is too rough, head gasket sealing is compromised.
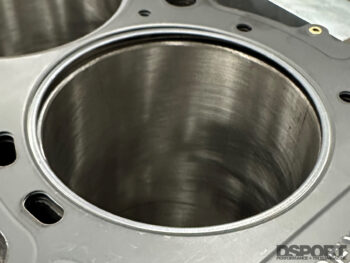
Copper Head Gaskets
Proven for over a half a century in competition, copper head gaskets have allowed many competition engines to set performance records. When teamed with stainless steel O-rings for combustion chamber sealing, copper head gaskets have proven to seal where other can fail. However, the O-rings require special machining of the block and/or cylinder head to accommodate the ring. This means changing over from a composite or MLS head gasket to a copper head gasket is not a drop-in a air. Instead, the decision to go copper should be made when planning the “build” of the engine.
Unlike MLS head gaskets that may only be offered in a couple bore sizes and two or three thicknesses, copper head gaskets can be made to a custom bore size and many different thicknesses. For example, SCE offers eight different thicknesses between 0.5mm and 2.3mm on its import applications.
With the 0.043” thick head gasket, SCE Gaskets recommends that the O-ring groove be cut into the block so that 0.008-to-0.0010” of wire is protruding above the deck. For extreme boost levels, SCE Gaskets recommends machining the O-ring retaining ring in the block along with a receiver groove in the head. We aren’t planning to go too crazy on Project Talon, so we opted for the non-receiver arrangement. While the SCE Pro Copper head gaskets can be used with rougher surfaces (up to Ra values of 100), we treated both the head and block to surface grinding, producing fine surface finishes in the 10-15 Ra range.
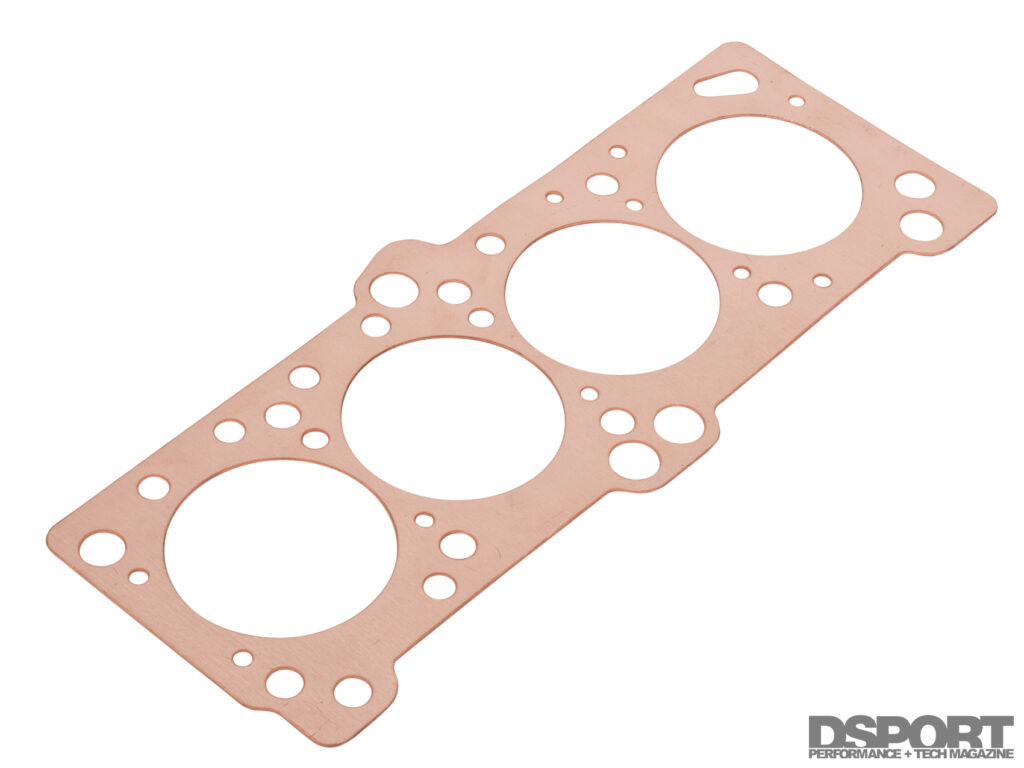
Our Test Bed
In years past, we hadn’t had an opportunity to use a copper head gasket. As we were planning out the rebuild of Project Talon’s 6-bolt 4G63 engine, we found the perfect candidate. When Project Talon was alive, it was running a factory composite head gasket along with stainless-steel O-rings. While that seemed OK at the 450whp level that was “serious” back in 1999, a truly serious power output today would be well into the 600whp level. Since the block already had O-ring receiver grooves, it made sense to go the copper head gasket route. We opted for an SCE Pro Copper head gasket with a 0.043” thickness that was optimized for our 85.75mm bore. Since our pistons were protruding 0.010” above the deck surface, the 0.043” gasket provides a quench/squish clearance of 0.033”, which is ideal.
On assembly, use the torque recommendation for the fasteners being used. In this case, we used ARP head studs and followed the recommended settings. SCE Gaskets recommends that the cylinder head be re-torqued a er the first heat cycle. According to SCE Gaskets, “Start the engine and allow it to reach operating temperature without placing any load on the engine. Shut down and allow the engine to cool to ambient temperature (over-night). With the engine cold and following the recommended torque sequence, one at a time back each fastener o just enough to relieve the friction set, then re-torque to specified torque value.” Once Project Talon is ready for the engine, we look forward to a long-term evaluation.
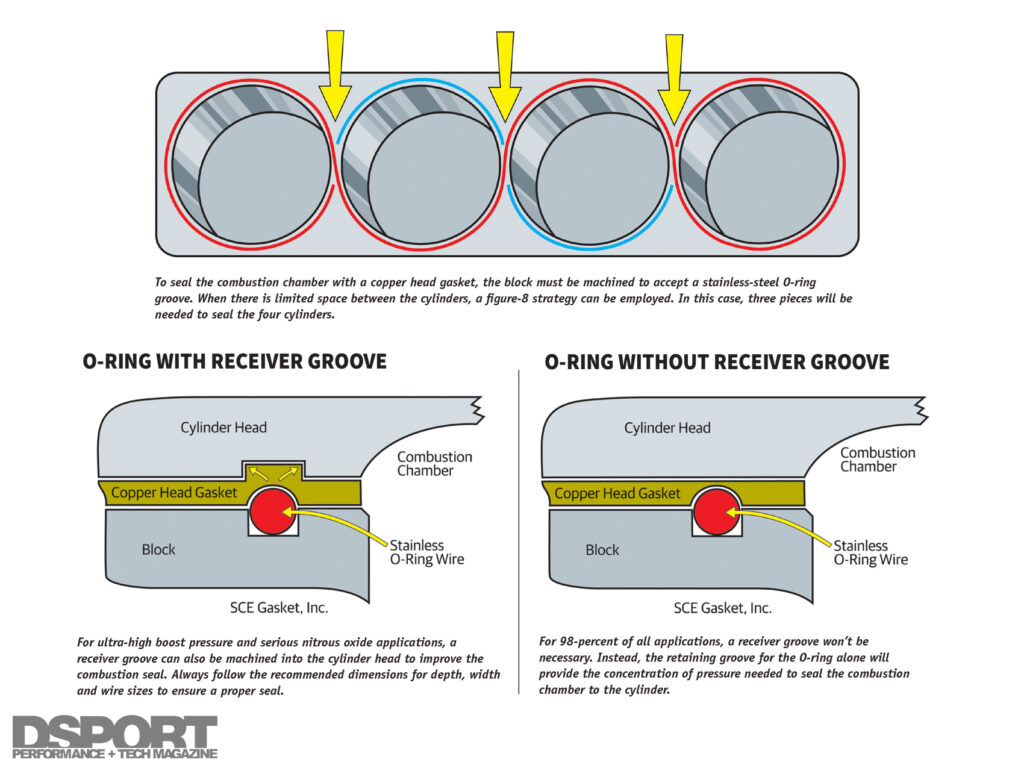
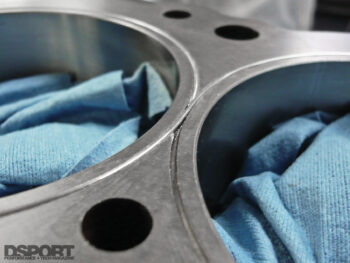
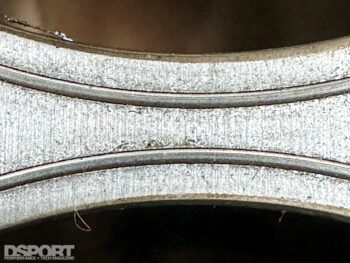
The Bottom Line
Head gaskets have far from an easy life. They seal the combustion chamber to the cylinder, the coolant passages from the block to the head, the oil drain back from the head to the block and the pressurized oil from the block to head. Worst of all, they get no appreciation when they work well. But, they are the subjects of swearing sessions when they fail. Factory composite gaskets should be avoided for all high-performance builds. High-quality MLS or copper gaskets are the solution for high-output applications. Understanding the capabilities and considerations for using these gaskets is a must to ensure good results.
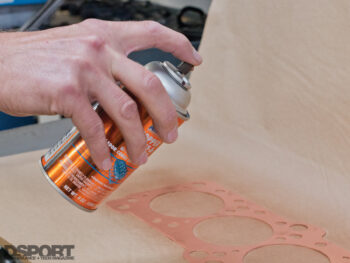
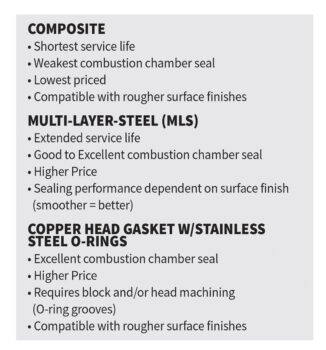