Solenoids Wet and Dry
DSPORT Issue #253
Text by Michael Ferrara // Photos by Joe Singleton
Nothing good ever comes from solenoid failure. When a nitrous oxide solenoid fails to open, engine performance suffers significantly. Fuel from the “wet” system or the additional fuel provided by the injectors on a “dry” system establish a fuel rich condition that drowns away performance. The higher the horsepower “shot” the system is jetted to produce, the worse the resulting drop in performance when the nitrous solenoid fails to open. While a nitrous oxide solenoid failure can lead to poor performance and a lost race, a fuel solenoid failure can result in much worse. On a “wet” nitrous oxide system, the engine is dependent on the proper opening of the fuel solenoid to provide the necessary amount of fuel to have a proper air-fuel ratio when the nitrous oxide is injected. If the nitrous oxide gets put into the engine but the fuel solenoid fails to open, a fuel-lean condition results. This fuel-lean condition can cause extreme in-cylinder temperatures that melt pistons, combustion chambers, valves and cylinders. With proper maintenance and proper system design, solenoid failure can be extremely unlikely and even harmless in some configurations.
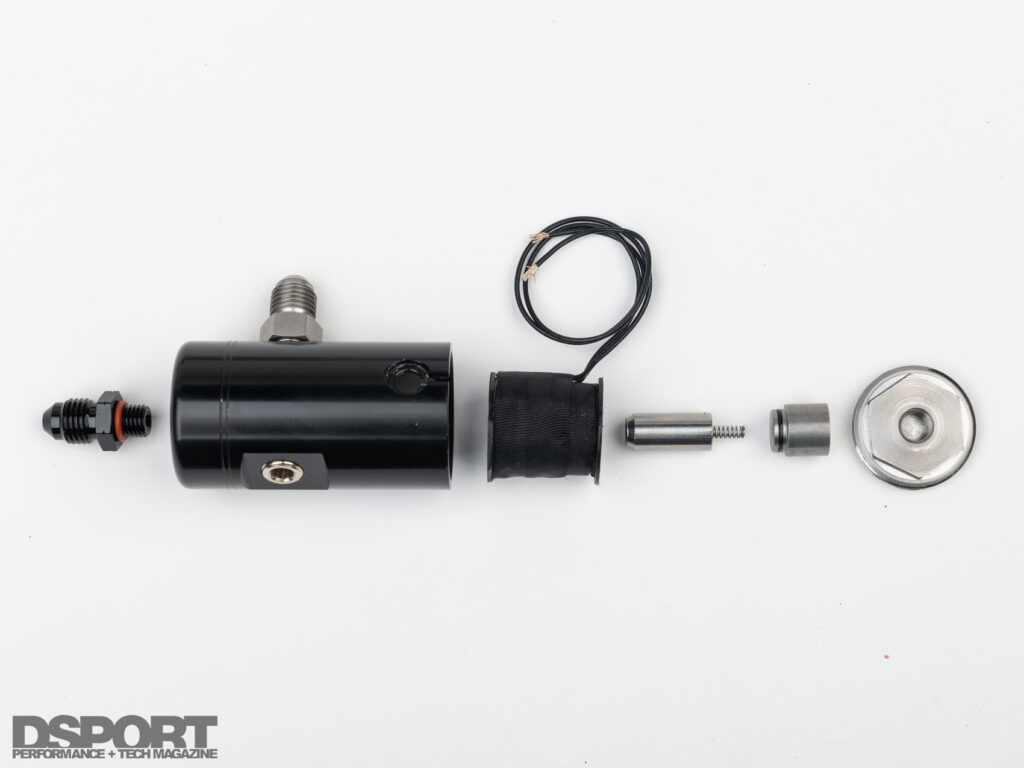
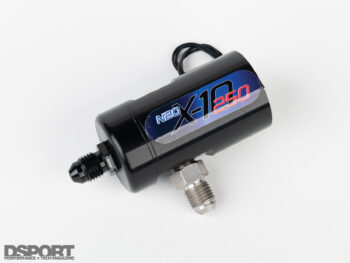
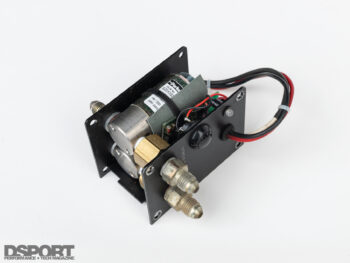
Dry vs. Wet Systems
On “dry” nitrous oxide systems, there will only be a nitrous oxide solenoid and no fuel solenoid. On these systems, the additional fuel required when the nitrous oxide is injected into the engine is supplied through the fuel injectors. The fuel injectors will either have their duty cycle increased to stay open longer to deliver the fuel or the fuel pressure feeding the injectors will be bumped up to deliver additional fuel.
On “wet” nitrous oxide systems, there will be both a nitrous oxide and a fuel solenoid. When the system is activated, both the nitrous oxide and fuel solenoid will be energized to open and both fuel and nitrous oxide will be flowing. Originally, individual nozzles for the nitrous oxide and fuel were the common setup but for the past few decades “fogger” type nozzles that combine the nitrous oxide and fuel have become much more popular. These “fogger” type nozzles have significantly improved over the years to aid in the mixing of fuel and nitrous oxide. If you are running a “wet” nitrous oxide system, consider using fogger type nozzle or the latest generation plates that have been engineered for improved nitrous and fuel distribution. This will work much better than individual nitrous oxide and fuel nozzles plus you will cut the number of holes you need to make in half.
What is a Solenoid?
Both nitrous oxide and fuel solenoids serve the same basic function. The solenoid acts a control valve that can be in an open or closed position to allow the flow of nitrous oxide or fuel to the nitrous oxide or fuel nozzles in the nitrous oxide system. The activation or control of the solenoid is accomplished by supplying 12 volts to the coil of the solenoid to change it from its normally closed condition to its momentarily on condition (whenever 12 volts is being fed to the solenoid’s coil). That’s about all that is common amongst all solenoids used in nitrous oxide systems.
Difference #1: Current Demands
Different solenoids will use different coils to achieve a desired level of performance. The design of the solenoid and the type of coil used will affect the current demands of that solenoid. As a result, every solenoid design will have different current demands and recommendations. In general, solenoids used for nitrous oxide will have higher current demands as they must operate the valve section at pressures that could be 1,100psi or higher. A typical nitrous oxide solenoid will pull about 10-12 amps of current while some larger ones may pull 15-20amps. A typical fuel solenoid may only pull 6-10amps. Before you wire up your solenoids, make sure you follow the recommendations for the size of the wire at the rating of the relay that should be used. If you are using nitrous oxide on an application where the system is activated repeatedly or for longer duration, the coils will tend to heat up as they do not have enough time to cool. As the coil heats up, current demands will increase so plan accordingly.
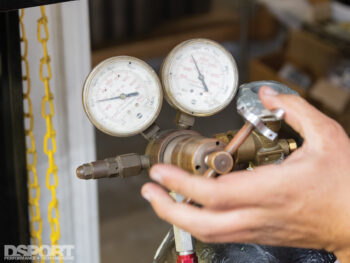
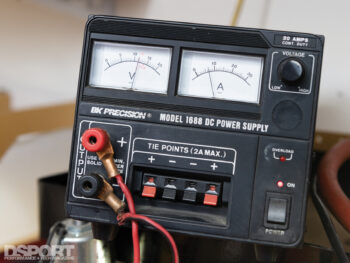
Difference #2: Horsepower Rating
While it sounds simple enough to rate solenoids based on horsepower rating, the reality is that several factors go into determining the horsepower capabilities of a solenoid. The solenoid’s inlet size, outlet size, inlet/outlet configuration, orifice size and amount of lift along with the operating pressure of the nitrous oxide or fuel will all influence how much horsepower a particular solenoid can support. Inlet sizes are either 1/8”NPT or ¼”NPT. Nearly all solenoids capable of supporting over 200hp will use the larger ¼”NPT inlet. While the ¼”NPT may only sound like its twice as big, the area is actually 4 times larger than the smaller 1/8”NPT. As for the outlet, 1/8”NPT outlets are the most common. These 1/8”NPT outlet can be found on solenoids that support up to 600 horsepower. The big ¼”NPT outlet is only found on some 1,000 horsepower nitrous oxide solenoids. When comparing solenoids, you may also notice that some solenoids feature a bottom dump as opposed to the original side-to-side configuration. The bottom dump design cuts the number of internal bends in half compared to a side-to-side configuration. By reducing internal restrictions, the effective pressure of the nitrous oxide at the discharge can be increased. Hence, solenoids with a bottom dump should be considered a superior design, all other factors being equal.
Solenoids also have an internal orifice size that is often provided in the manufacturer’s specifications. The orifice can be thought of as the internal jet size of the solenoid. In nearly all cases, the orifice will be smaller than the inlet and outlet on the solenoid. When this is not the case, the inlet or outlet size may determine the horsepower potential of the solenoid instead of the orifice.
The typical entry-level nitrous oxide system usually features a nitrous solenoid with 1/8”NPT inlet, 1/8”NPT outlet and an orifice sized around 0.075”-0.085”. These solenoids will typically be rated to supply nitrous oxide systems jetted to deliver 150-200 horsepower shots.
Most uprated nitrous oxide solenoids will feature ¼”NPT inlets with 1/8”NPT outlets. Orifices will usually be in between 0.090” and 0.125” in size. These solenoids will support nitrous oxide flows between 200 and 600hp. There are also larger nitrous oxide solenoids that have ¼”NPT inlets and outlets with orifices in the 0.250” range. These can support 1,000hp or more.
If you find two solenoids with similar inlet and outlets, similar orifices but different horsepower ratings, the reason could be tied to the inlet/outlift configuration and the amount of lift in the solenoid. Few manufacturers will specify the amount of lift and only a few solenoids have adjustable lift. One reason is that when the horsepower potential and the rest of the specifications are known, there isn’t really a need to know the lift. However, the amount of lift can influence how well the solenoid performs when it is “pulsed” in a progressive nitrous system. Some solenoids will specifically state that they are not compatible with a controller while others may be purposely designed for such applications.
The Pulsoid X-10 solenoids from Wizards of Nitrous have an adjustable seat. This seat is set from the factory at the highest recommended lift but it can be dialed back to restrict flow in the solenoid to anywhere between 20 to 100 percent of its maximum flow. To adjust the lift, you simply remove the outlet fitting and then you can use a flat blade screwdriver to make adjustments. In the case of the X-10 250bhp solenoid, the orifice size is 0.091” while the preset lift is 0.026”. This results in a maximum flow of 916lbs/hr of liquid nitrous oxide. Making a ¼-turn adjustment reduces the lift to 0.016” which in turn limits flow to 791 lbs/hr. This drops the flow of the solenoid from 250bhp to 215bhp. Another ¼-turn adjustment reduces the lift to just 0.006”. At that lift the nitrous solenoid only flows enough to support 105bhp.
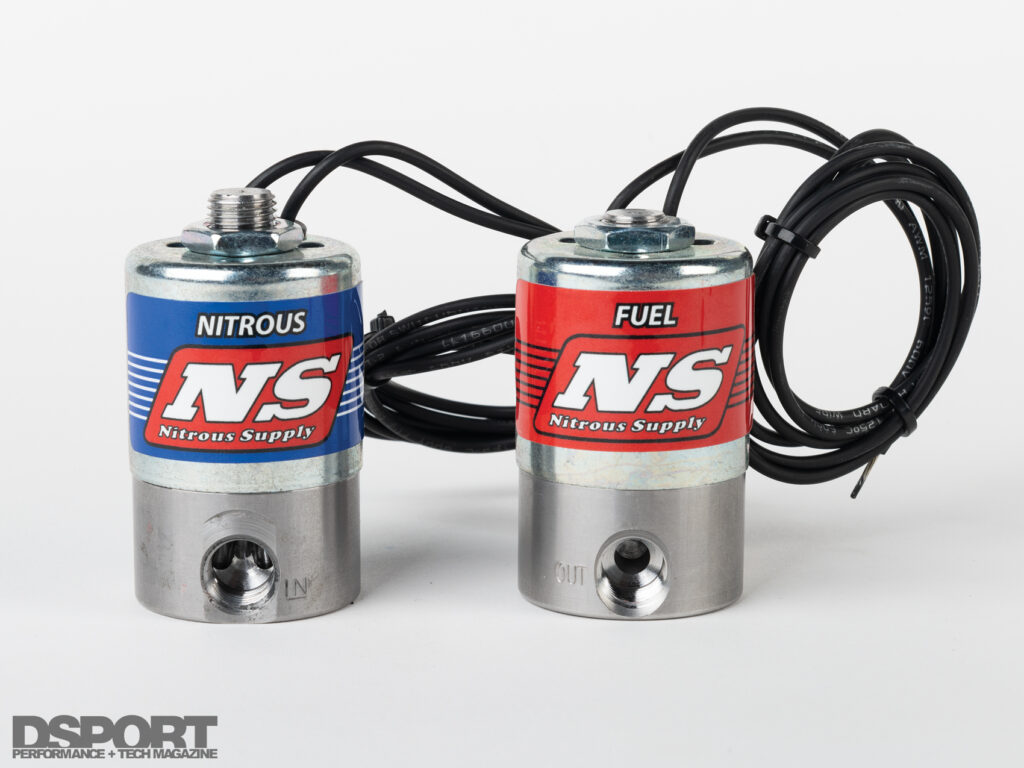
Difference #3: Materials and Design
Most solenoids are constructed from stainless steel and mild steel while some are made from aircraft grade aluminum. The more common stainless/mild steel construction solenoids feature a design that will require maintenance while some premium solenoids made from aluminum, like the Pulsoid X-10 from Wizards of Nitrous, claim that the solenoid is maintenance free. Aluminum body solenoid will tend to be lighter than stainless steel and will dissipate the heat from the coil better. Essentially, solenoids like the Pulsoid X-10 were designed specifically for pulsed use on a nitrous oxide system whereas many other solenoids are repurposed or upgraded repurposed valves for nitrous oxide use. If you are planning to set up your nitrous system to deliver a progressive amount of nitrous by way of pulsing the solenoid, you may want to consider a solenoid designed specifically for that purpose. At the very least, increase the service interval on your conventional solenoids when use for that purpose.
Solenoid Selection
Since you don’t want the solenoid to be acting like the jet for your nitrous oxide system, it is always a good idea to use a solenoid that is rated about 50 percent higher than your planned shot. If you are planning to use a 100hp-shot of nitrous oxide, selecting a solenoid that supports 150hp or more is a good choice. If you are planning on using a 160hp-shot, using a solenoid rated for 250bhp will make sure that the solenoid isn’t the bottle neck in your system. We set up a few charts showing the 1.5:1 ratio and a 1:1 ratio of solenoid orifice size to jet size based on the number of nitrous oxide jets used. If your jets are larger than the 1:1 ratio for the size solenoid that you are using, you need to upgrade your solenoid to a higher-capacity unit. If your jets are the size listed in the 1.5:1 ratio chart or smaller, your solenoid is a good match. If your jetting falls in between the two charts, it’s a judgement call. It won’t hurt to go to a higher-capacity solenoid, but there may not be any appreciable gains.
Solenoid Failure
Solenoids have two main modes of failure. First, the most common failure of a solenoid is a failure to open. When a solenoid fails to open, there could be a few possible causes that we will discuss later. For now, let’s explore the results from a solenoid failing to open. On a dry nitrous oxide system, the failure to open of the nitrous oxide solenoid results in a fuel rich condition because additional fuel is still delivered into the engine while no nitrous oxide is injected because of the solenoid failure. On a wet nitrous oxide system, the failure of the nitrous oxide solenoid to open when the fuel solenoid does function correctly also results in the same fuel rich condition. Fuel is being added but no nitrous oxide is getting into the engine. While have a failure to open issue with a nitrous oxide solenoid can result in a significant drop in performance due to the excessive rich fuel mixture that results, no damage to the engine occurs. The worst result is probably a lost race.
Unfortunately, a failure to open solenoid issue on the fuel solenoid in a wet nitrous oxide system can result in catastrophic engine damage. In these cases, additional nitrous oxide flows into the engine without any additional fuel (since the fuel solenoid failed to open). The result is a fuel lean condition that can lead to extreme in-cylinder temperatures, detonation, pre-ignition and other conditions that melt spark plugs, pistons, valves, cylinder heads and blocks. If you have a wet system, always be sure that your fuel solenoid is properly maintained.
When a solenoid fails to close, there could be some serious consequences. If the fuel solenoid fails to close, fuel can continuously flow into the engine whenever fuel pressure is present. Normally, a small amount of fuel comes through the “fogger” nozzles because something is keeping the solenoid from fully closing. In extreme cases where the solenoid fails in a near fully open position a bunch of fuel may be added. This can cause a severe fuel rich condition or may even cause enough fuel to enter the engine that a hydro lock situation can occur.
When a nitrous oxide solenoid fails to close (an extreme rarity if you follow some basic rules), big problems are often the result. If nitrous oxide continues to flow when the driver and engine expect the system to shut off, many things can go wrong. When the nitrous oxide solenoid fails in the open position, the engine may become extremely fuel lean and many parts can get torched. Cylinder heads, spark plugs, pistons and engine blocks can all be melted. If the throttle closes, a giant nitrous backfire can occur in the manifold blowing off the throttle blades, intake manifolds and more. Fortunately, nearly all solenoid failures can be avoided by following some basic rules.
Avoiding Solenoid Failure
About 95% of all solenoid failures occur due to modification or the use of improper tools when servicing the solenoids. Just like it’s possible to drill out a nitrous oxide jet to get more flow (at the expense having a metered precise flow), modifications can be made to the solenoids to increase the flow potential.
Rule #1: DO NOT SWAP NITROUS AND FUEL SOLENOIDS.
Nitrous oxide and fuel solenoids are often made with different seal materials and different coils in order to function best with the product being used. When Teflon seals were first introduced into these solenoids, the harder Teflon worked great for fuel solenoids, but not very well on nitrous oxide solenoids. Today, softer Teflon formulations make them functional with nitrous oxide. Seal materials need to be not too soft and not too hard. They also need to be chemically compatible with the fluids that will flow through the solenoid. Solenoids need to maintain a bubble-tight seal. That means it can only allow for one small bubble to form every minute it is submerged in soapy water. Proper sealing can only be achieved when nitrous oxide solenoids are used for nitrous oxide and fuel solenoids are used for the recommended fuels. In addition, fuel and nitrous oxide solenoids often use different coils. Since fuel pressure is usually in the 35-to-90 psi range when the nitrous oxide system is activated, the solenoid can be opened with a less powerful coil than the one required to open the nitrous oxide solenoid when the nitrous oxide pressure is at 1,000psi.
Rule #2: DO NOT MODIFY THE SOLENOIDS IN ANY WAY.
If the solenoid that you purchased doesn’t have the flow rating that you need, spend the money on getting a new solenoid that meets your requirements. While drilling the internal orifice to a larger diameter will increase the flow through the solenoid, it will also require more power from the coil to open the solenoid. The increase in current required at the coil can overheat the coil or cause it to fail. This will result in a failure to open situation. High-quality nitrous solenoids from reputable manufacturers have a balanced coil for the solenoid design. Some people also use upgraded coils on the solenoid to get them to open at higher running pressures. Again, DO NOT MODIFY any portion of the solenoid. Run the solenoids as designed and they will give you a long service life.
Rule #3: USE THE PROPER TOOLS AND PROCEDURE WHEN SERVICING SOLENOIDS.
Depending on how often you activate your solenoids, the period that you have them open and whether or not you are pulsing your solenoids will all factor into how often you should service your solenoids. For those new to nitrous oxide, you may want to consider sending in your solenoids to get serviced, instead of doing it yourself at least for the first service. If you make your first service interval 12-, 18- or 24-months, you can ask the expert rebuilding your solenoids if you need to extend or shorten the service interval. After that, purchase the proper tools and rebuild the solenoids yourself if you want to save a few dollars and cut down on the down time while the solenoids are in transit. It’s good to rebuild your solenoids at least once to be able to perform an emergency service in the field if you have issues at a race. If you don’t have the proper tools to disassemble the solenoids for service and if you don’t properly clean the parts, you are likely to run into issues with the solenoids. Getting dirt or other contaminants in the solenoid can cause failures to close and a host of other issues while improper tools can damage shafts and reduce lift or cause binding issues with the solenoid.
Rule #4: FILTER THE FUEL AND FILTER THE NITROUS.
The most common reason for a solenoid failing to close is that some foreign contaminant is affecting the seal. The easiest was to avoid this is to simply have a filter in place before the solenoids. On modern fuel injection applications, the OEM fuel filter is often located just before the supply for the solenoid. If this is the case, there isn’t a need to add an additional filter. However, on fuel injected applications that don’t have a fuel filter integrated near the pickup location for the fuel supply to the solenoid, a filter should be added. This also holds for carbureted applications. On the nitrous side, installing a filter just before the solenoid is recommended. With this location of the filter, there won’t be a chance for contaminants that enter the line during bottle swaps to affect the solenoids as the filter just before the solenoid will capture the contaminant.
Rule #5: DON’T WIRE FOR FIRE.
Always run the proper size wire, select proper current relays and make proper connections to avoid shorts. Cheap relays can fail under high G launches or high G deceleration when the parachute is pulled. Only use high-quality made in USA/Germany/Japan relays. Better yet, consider upgrading to solid-state relays to eliminate this potential failure all together.
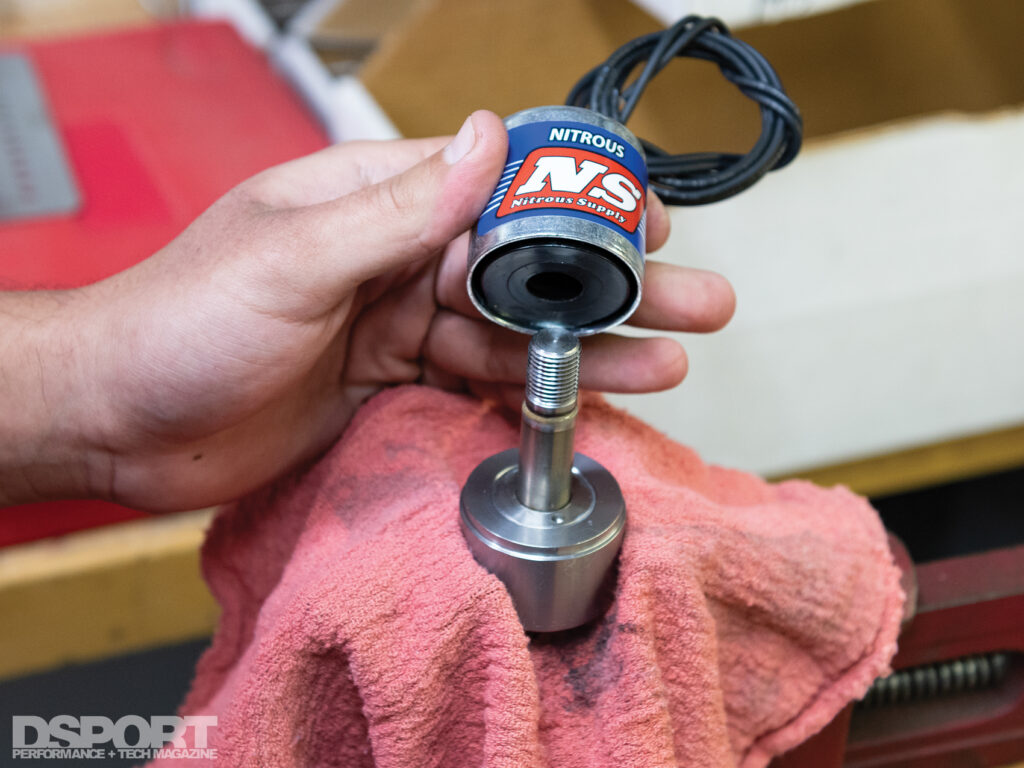
The Bottom Line
When Nitrous Oxide Systems co-founder Mike Thermos was initially sourcing solenoids when the company started, one engineer said of the sample provided, “You can’t use that solenoid in a cryogenic application, it will fail.” At the time, that sample solenoid was the most popular one in use by 10,000RPM, Marvin Miller and a host of the other first-generation nitrous oxide system manufacturers. When Mike responded, “Everyone seems to be using this one and it seems to work fine. What do you mean?” The engineer continued to say there was no way that the solenoid would survive 1 million cycles of use at a 50-percent duty cycle. When Mike explained that the solenoid would normally see only a couple hundred cyclers before being serviced, the engineer took a new stance and said, “if it only needs to operate for that long, it should do it,” The solenoids are the work horses of the nitrous oxide system. With proper selection, care and feeding, the solenoids can provide a lifetime of use when properly serviced. Premium solenoids made specifically for cryogenic operation can provide a lifetime of use without the need to service. However, adhering to the five rules is a must regardless of what solenoids are being used. Next month, we take a look at the control of these solenoids under pulsed operation for progressive nitrous oxide delivery for smooth power boosts.
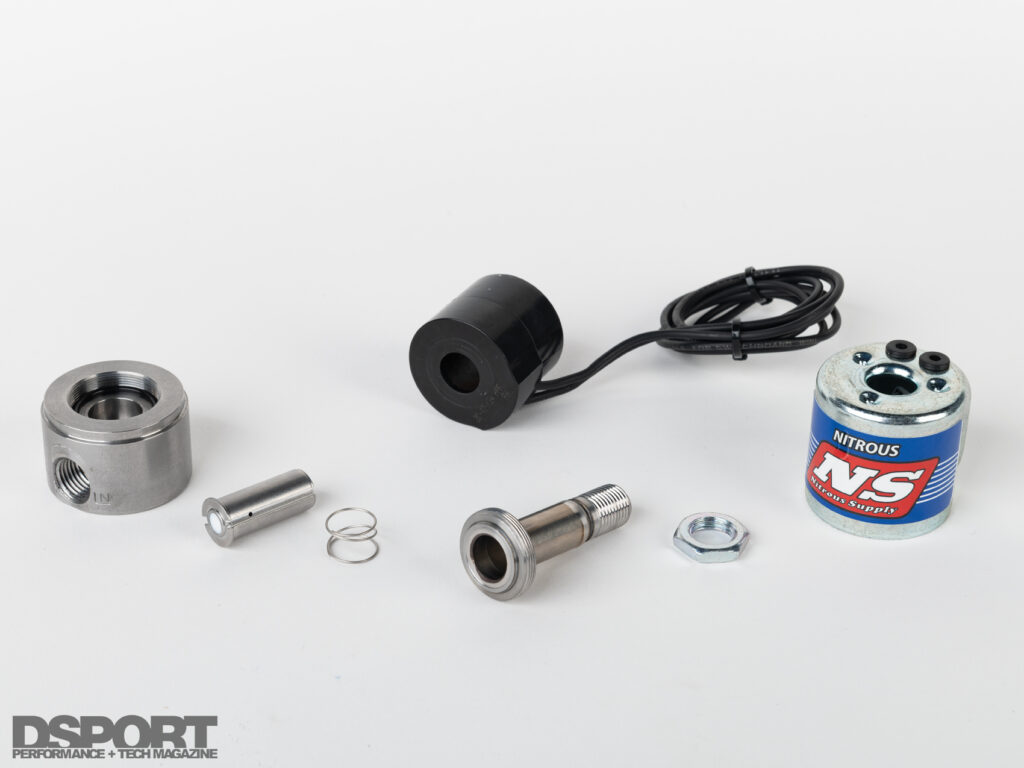