TAKE TWO NEARLY IDENTICAL VEHICLES equipped with the same drivetrain, brakes, suspension, and aero. Set both vehicles to have the same exact final weight and weight balance. If the only difference is the rigidity of the chassis, do you think it will make a difference on the race track or the street? Ask any experienced race car builder or even OEM vehicle designer and the answer will be a definitive “yes.” All other factors being equal, the higher the rigidity of the chassis, the quicker the car will be around a racetrack. If that’s not reason enough to consider improving the rigidity of your project car’s chassis, consider that vehicle control will also benefit, as well as the overall safety of the vehicle.
By Michael Ferrara // Photos by Richard Fong
DSPORT Issue #148
A custom-fit, weld-in roll cage provides the most significant increase in chassis rigidity. Bolt-in roll bars and cages are best suited for show cars.
Why Go Stiff?
So the promise of better performance, improved vehicle control and increased safety warrants attention, but just how does a more rigid chassis make all that happen? Quite simply, a rigid chassis provides a more stable foundation for your vehicle’s suspension. By minimizing the flex in the chassis, the suspension takes control of keeping the tires in contact with the road surface. When there is flex in the chassis, the chassis itself works as an unpredictable fifth spring in your suspension. This flexing of the chassis can create a vehicle that stores and releases the energy stored in the sprung chassis at the least opportune moments. The end effect is a vehicle that exhibits delayed steering response, reduced cornering ability and sometimes a mind of its own. When a chassis flexes during cornering, this flex can pull the steering components to affect the alignment toe settings. These changes in toe can change. These changes can actually steer the vehicle, giving it the mind of its own attitude. To compensate for the flex-induced changes to suspension alignment, the driver must counter the resulting chassis steer scrubbing away speed. Of course, a car that steers on its own also decreases the driver’s control of the vehicle and its overall safety.
Making it Stiff: Starting Point
Once convinced that increased chassis rigidity is desirable, the next logical step is to explore how to make the chassis more rigid. All of today’s performance vehicles are built on a “unibody” design, as opposed to the body-over-frame design that was used almost exclusively up through the 1950s and 1960s. With a unibody, the body or shell of the vehicle functions as the frame and structure for the vehicle. The design of the roof, floor, pillars and accompanying chassis bracing all affect the chassis rigidity of the vehicle.
As computer modeling, metallurgy and manufacturing techniques continue to advance, nearly every new generation of a vehicle is able to be touted as having a double-digit increase in chassis rigidity. Hence, the first step is to start with the most rigid chassis that you can find to build upon.
This particular roll cage offers a sophisticated lattice array of bars that tie in many points of the cabin in order to make the chassis as rigid as possible. Excellent for a racecar, not practical for a streetcar.
The Triangle Offense
The geometric reality of increased rigidity is usually found in the shape of a triangle. The triangle represents the simplest, lightest and most rigid frame structure. In both nature and construction, examples of triangles make up rigid structures. Whether the component is a roll bar or a simple strut tower brace, the use of triangle geometry provides peak rigidity increases for minimal weight.
Ladder braces sometimes tie together sub-frame members all the way back to mid-chassis.
Practical Street Solutions
A weld-in roll cage or stitch welding the chassis are proven ways to increase the rigidity of a chassis. However, neither is practical for most street cars. Instead, practical solutions come in the form of “bolt-on” strut tower braces, chassis braces and bolt-in roll bars.
The simplest strut tower brace simply connects the left and right strut towers with a rigid link that significantly reduces the flex of the tops of the strut tower. This flex normally occurs when only one of the two front or rear wheels encounter a bump that drives a force up through the strut toward the top of the strut tower as the spring and damper are compressed. Without a strut tower brace in place, the result is that the top of the strut tower flexes closer to the opposite strut tower during this compression phase. The flexing of the chassis also stores energy which is released when the suspension rebounds to keep the wheel in contact with the road on the backside of the bump. Here the tower may now move further away from the other tower during this rebound. This movement in the shock tower can cause other steering links and suspension members to move affecting alignment and steering. Hence, the basic strut tower brace accomplishes a great deal, despite its simple design. More complicated strut tower braces that not only tie the strut towers together but also triangulate the brace to the firewall, improve chassis rigidity by reducing the maximum deflection of the portion of the chassis between the firewall and the shock tower.
Under-chassis braces include lower tie bars, sub-frame braces, and ladder braces. The purpose of many of these braces is to improve the rigidity of the suspension member mounting point. Since all forces applied to the chassis enter through the suspension and subframe, increasing the rigidity of the mounting points often pays big dividends. The lattice design of most subframe braces helps to reduce the flex that the subframe, the chassis and the point at which they join the experience. Lower tie bars also supplement the subframe by joining the pivot points of the lower suspension arms, eliminating yet another variable from the suspension geometry puzzle. Though not as popular as strut tower braces or chassis braces, the installation of aftermarket fender braces in front of the door hinges underneath the front fenders can also help to eliminate flex.
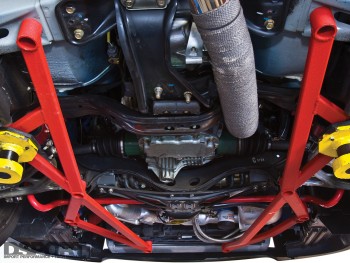
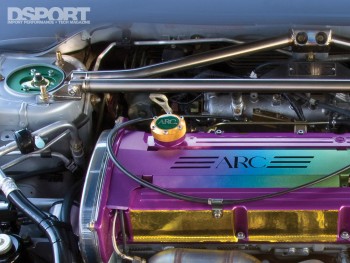
Last, but not least, a properly designed bolt-in roll bar or roll cage can also increase chassis rigidity. However, most serious performance enthusiasts view bolt-in roll cages as they do two-inch harnesses. Both are half-ass solutions. If you are going to live with the inconvenience to entry and egress that a roll bar or cage exhibits, simply get a custom weld-in cage that fits your vehicle and the type of motorsport that you enjoy.
Full-Race Recommendations
There are no serious race vehicles without a weld-in roll cage. Properly designed to meet the specifications provided by the sanctioning body of the motorsport, a weld-in full cage will significantly increase chassis rigidity while also providing additional driver safety in the event of a roll over or crash. If you are building a racecar from the ground up, you may also want to consider stitch welding or riveting the entire unibody structure. Stitch welding or riveting the overlapping seams of metal will increase the overall rigidity of the chassis without adding any additional weight.
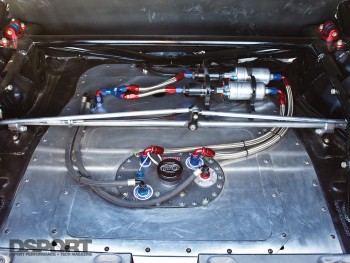
Here is a weld-in rear strut-tower brace that includes two additional bars that tie in the rear corners of the body, unifying the panels that compose the trunk compartment. The rear kickers of the cage also join at the rear shock towers
The Bottom Line
The more rigid the chassis, the quicker it will be on the track or at the strip. In addition, improving chassis rigidity will make for a vehicle that will be easier to control as the suspension is able to do its job with maximum efficiency and predictability. From first-hand experience, we’ve witnessed the improvements with everything from a simple set of front and rear strut tower braces to a weld-in roll cage. A vehicle with improved chassis rigidity simply becomes more enjoyable to drive as it responds better to driver input while requiring less driving effort. Of course, one must consider an ultimate limit to chassis rigidity. Can a chassis be tweaked to be too rigid? Probably not. Chances are that none of the recommendations provided in Chassis 101 would take it too far, so plan your strategy accordingly. Remember that the chassis is the backbone of the vehicle that provides the foundation for every other system on the vehicle. While aftermarket performance braces don’t show a performance improvement that’s easily verified on a dyno, they can often be felt in normal street driving or verified on a timed road course.
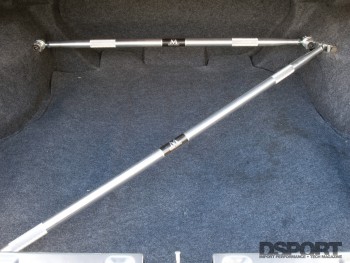
Making it Stiff Checklist
1. Start with the newest generation of the vehicle that your budget will allow. For example, a 370Z would be a superior foundation to a 350Z, based on chassis rigidity.
2. Consider aftermarket strut tower braces for any vehicle not equipped with OEM strut tower braces or vehicles equipped with factory strut braces that flex.
3. Use bolt-on chassis bracing that reinforces suspension or subframe attachment points for largest increases in chassis rigidity.
4. When comparing braces of similar construction, triangulated designs will deliver improved rigidity.
5. Avoid bolt-in roll bars and roll cages. When it’s time to step it up, spend the money on a custom weld-in roll cage that meets the sanctioning body requirements for the vehicle.
6. Don’t be one-sided. Improve chassis rigidity at both the front and rear of the vehicle to avoid a squirmy chassis.
7. A stitch saves time. If you are building a vehicle from the bare shell, consider stitch welding or riveting the entire unibody structure wherever the sheet metal overlaps.