Titanium. It not only delivers exceptional performance, it also sports an unmistakable look. Even the name “titanium” sounds cool. For years, titanium parts have been something that everyone wants, but not everyone can afford. A few years back, TOMEI USA started offering titanium cat-back exhaust systems at pricing that was less than half the going rate. Today, TOMEI USA titanium cat-back exhaust systems are amongst the most popular in the import performance community. Recently, TOMEI USA introduced a titanium front pipe for the Nissan RB26DETT Skyline GT-Rs. While this product is an exceptional piece on its own, the number of RB26 owners worldwide is limited. Fortunately, the technology behind this product will soon be applied to more applications. This means more titanium front pipes, up-pipes and downpipes from TOMEI USA at affordable prices in the months and years to come.
By Michael Ferrara // Photos courtesy of TOMEI USA
DSPORT Issue #223
To allow for expansion and proper fitment, the TOMEI USA Titanium RB26 Front Pipe consists of 4 sections. Slip fits, springs, band clamps and flanges are used to make the connections.
Obtainable Titanium
TOMEI USA pioneered the development of affordable titanium high-performance exhaust systems a few years ago. These systems came in at only 25-to-50% of the retail cost of other titanium exhaust systems on the market while not cutting any corners on quality. The reason for the dramatic cost reduction was simple. Whereas most high-performance titanium exhaust systems were manufactured from standard shelf-stock titanium alloy tubing, TOMEI USA took a different approach. TOMEI USA worked with a manufacturer to produce custom titanium alloy tubing. The wall thickness, alloy composition and heat treatment of the titanium alloy supplied allowed not only for easier manufacturing, but also a higher-quality finished product that featured an even lighter weight.
Click here to order yours today >>
Lobster Tails and Pie Cuts
If you have ever looked at anything made from titanium tubing (exhaust system, intake pipe, etc.), you may have noticed that bent sections are made up of sections of pipes that has been cut at an angle to produce a cross-section similar to a slice of pie and then welded back together. The outcome of welding these pie cuts together shares a similar appearance to a lobster tail. In the case of an entire exhaust system, the number of welds to account for these bends can be extensive. For example, the 94mm GReddy titanium exhaust system on our Project R35 sports no less than 86 welds. While these welds when done properly can look and perform exceptionally well, they do have drawbacks. Bad welds can crack or disrupt airflow and the high number of welds needed when pie cuts are used results in an extremely high production cost.
Prototype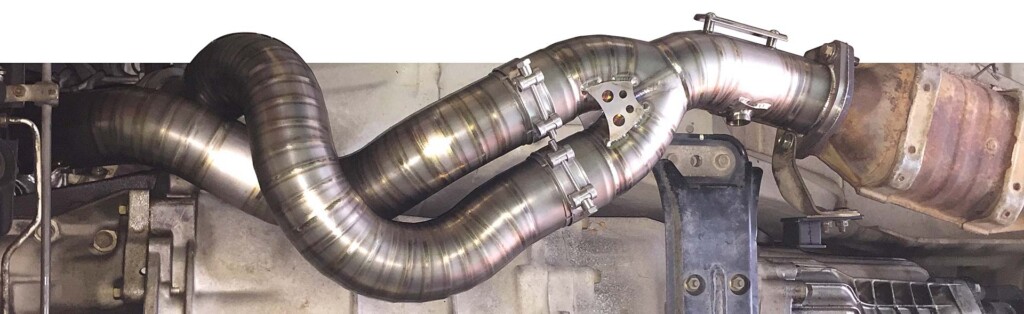
The prototype of the Titanium RB26 Front Pipe uses conventional pie cut sections to make all of the bends. This process takes over twice as long as the production unit which features mandrel-bent sections.
Production
The production version looks remarkably cleaner and is less likely prone to failure of a weld under extreme conditions. Less manufacturing time means lower price.
Get Bent
With most high-performance stainless-steel exhaust systems, machines can be used to mandrel bend the exhaust tubing to its final shape for each section. As a result, the only welds needed are those to flange, bung or bracket in most cases. Unfortunately, titanium alloys are not very cooperative on conventional mandrel bending machines with the bending tooling used for stainless steel. Take a straight piece of titanium alloy tubing and run it in a conventional mandrel tube bender and chances are that you will end up with cracks, thin spots and wrinkles. However, if the titanium could be bent and maintain a specified wall thickness and shape, the advantage would be increased durability. The durability would be significantly improved in conditions that are extremely stressful to welds. These stressful conditions would include areas where even higher temperatures are experienced than in a cat-back exhaust system. Specifically, it would be ideal to use a bent section (instead of welded) in the most highly stressed areas of the exhaust system. This would include the downpipe sections of the exhaust.
Bigger is better, especially when it comes to downpipe diameter on a turbocharged vehicle. The larger diameter pipes reduce exhaust back pressure. This improves boost response and reduces pumping losses to add power.
Mash-Up Solution
When TOMEI USA set out to design a new downpipe for the RB26, they wanted to offer a premium titanium offering for Japan’s flagship performance vehicle. In the process of building prototypes, engineers recognized that a significant number of welds was needed in order to provide a low-restriction path for exhaust flow that fit the engine and chassis space limitations. Since these same engineers were also experienced in designing stainless steel downpipes that featured mandrel-bent tubing with minimal welds, a “what if” moment soon followed. While the engineers knew that there was no known way to bend the entire length of the downpipe in titanium without having thin spots, wrinkles or cracks, they considered “What if we designed some specialized bending tooling that could bend some sections of the system and combine this with conventional pie-cut sections as needed?” The TOMEI USA Titanium Front Pipe for the RB26 engine is the first product to roll out using this combined manufacturing approach. For this application, tooling was built to allow the sections subjected to the highest thermal stress and strain to be bent rather than welded. This approach delivers a product with increased durability while also cutting the manufacturing time in half. TOMEI USA was so pleased with this R&D and manufacturing experience that they are planning to incorporate the process on more titanium products soon.
TOMEI USA Titanium RB26 Front Pipe
Response and power. With turbocharged vehicles, there are many upgrades that can deliver an increase in response or power. Many times, an increase in one of these comes at the expense of a decrease in the other. Moving to a bigger turbo might give you more power potential, but it might also sacrifice boost response. Fortunately, there are performance upgrades for turbocharged cars that do provide improvements in both response and power. The largest category of these upgrades focus on reducing exhaust restrictions. Less exhaust backpressure allows the turbo to spool up faster to the target boost pressure level and reduced exhaust manifold pressures allow the engine to produce more torque and horsepower.
After the OEM cat-back exhaust system, replacing the OEM front pipe on the R32, R33 and R34 GT-R provides one of the best opportunities for improving exhaust flow. The OEM front pipe measures only 60mm in diameter when it connects to the turbo outlet of each turbo. These twin 60mm pipes merge into a single 70mm pipe. The TOMEI USA titanium front pipe uses 70mm entries that are 36-percent larger in cross-sectional area. These 70mm tubes step up to 76.3mm before merging into an 80mm exit that is over 30-percent larger in cross-sectional area over the 70mm OEM. These larger diameter pipes reduce back pressure in the exhaust system and allow for more power to be realized at a given boost level. The amount of power increase is going to be dependent upon which turbochargers are being used. Fortunately, the sizing of these pipes makes them ideal for any upgrade turbo that features a stock fitment or any aftermarket turbo kit that utilizes the OEM front pipe.
In addition to producing additional power, the TOMEI USA Full-Titanium Front Pipe Kit also reduces the weight of the front pipe by nearly 50-percent. While a 6.6-pound weight reduction may not be reason enough for some, the improved exhaust note alone may win some over. The oversized front pipes and the thin-wall titanium allow the RB26’s true voice to be heard.
The design of the TOMEI USA Full-Titanium Front Pipe Kit looks to be aimed at ease of installation and high durability. The front pipe kit consists of four main sections with slip fits to optimize fitment and to allow for thermal expansion of the engine and the front pipe at different expansion rates. The slip fits at the exhaust Y-section to primary pipes allow for the front pipe to be optimized for fitment in the chassis. These slip fits get cinched in place by band clamps. The slip fit at the front inlet is retained by springs. This design element eliminates any stresses or strains caused by changes in the turbo positions as the engine heats up.
The Titanium Advantage
As a material, the popular titanium alloy used in aerospace and automotive applications excels in its strength-to-weight ratio. Compared to 316-grade stainless steel, titanium alloy is three times stronger pound for pound. The famous SR-71, which made its first flight in 1964, still holds the manned aircraft top speed record. This aircraft’s structure was over 90-percent titanium alloy. In addition to an exceptional strength-to-weight ratio, titanium alloy is also extremely corrosion- and heat-resistant. It is also stiffer and more resistant to thermal shock compared to most other alloys. By just about any measure, titanium alloy is an awesome material.
Click here to order yours today >>
Titanium Challenges
Based on the price of titanium alloy parts in general, you would think that titanium is quite rare. In fact, titanium is the ninth most abundant element found in the earth’s crust. It is more abundant than zinc, tin, copper, lead or nickel. So, if titanium is not all that rare, why are titanium parts expensive? The reason for the high cost of titanium alloy has to do with the high-cost to manufacture the material and parts made from titanium alloy. Compared to other materials, titanium alloy can be extremely hard to machine and it can also be prone to fracture during most manufacturing processes.
The Bottom Line
When you consider the cost of getting custom piping built from titanium, the $1,090 MSRP for the TOMEI USA Full-Titanium Front Pipe Kit for RB26DETT is an insane value. While the street price of the kit may be an extra $300 over the cost of a quality stainless-steel front pipe, the weight reduction, sound improvement and bragging rights associated with a titanium front pipe will probably be worth the additional money for most. While we are very happy to see a quality new product for the RB26-powered GT-Rs come to market, we are even more excited to see how TOMEI USA uses its new manufacturing process to bring even more titanium products to the market.