Picking the Best Fuel for Your Engine
DSPORT Issue #226
Text By Michael Ferrara
One size never fits all and there is no one that is perfect for every application. When we visit a gas station, we usually have three or four different fuel options for the spark-ignited, internal combustion engine in our vehicle. When we choose to race, the selection becomes even broader. There are over a hundred different blends of racing gasoline, a dozen or more blends of racing ethanol, a couple methanol distillations and even that “top fuel” called nitromethane. Diving into this topic without a basic foundation of knowledge and a clear understanding of goals can lead to subpar results or in the worst case, complete engine failure. While there are countless specifications for each fuel, there are seven that are the most important to understand when it comes to selecting the ideal fuel for your application. Energy density, knock resistance, air/fuel ratio, total energy of combustion, cooling factor, and chemical considerations are the key factors that must be understood. Once understood, we can take a deeper look at how different fuels stack up in these categories in part two.
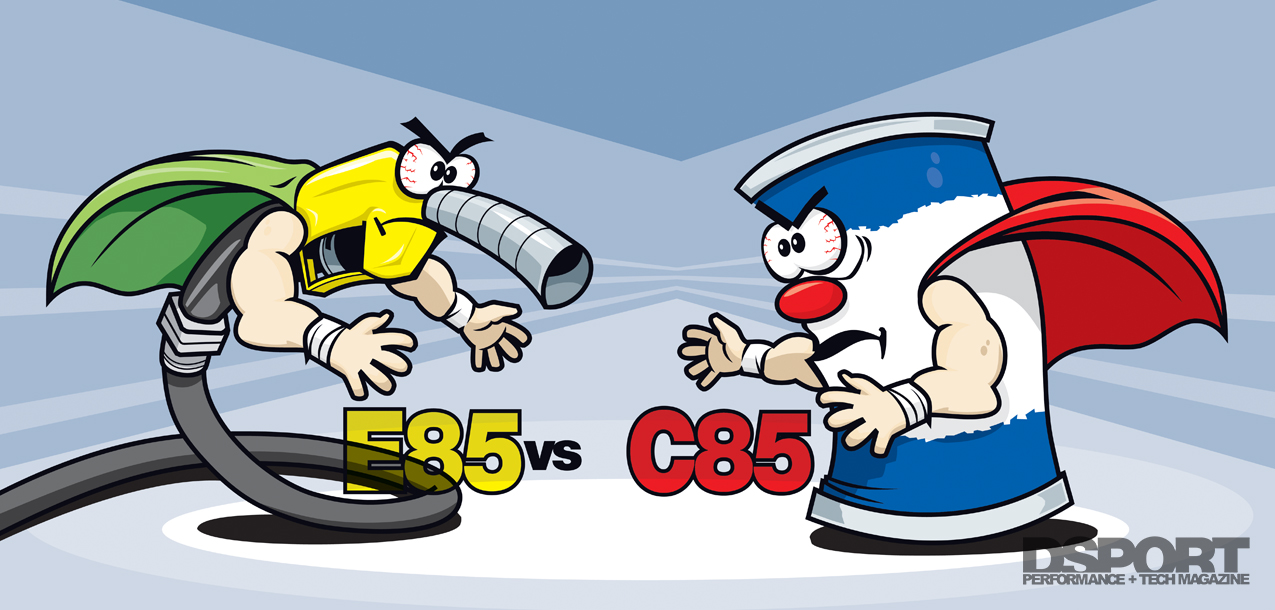
Energy Density: Bowl of Popcorn or Bowl of Pasta
Our bodies and your engine are both machines that require energy to run. Our body relies on calories from the food we eat while your engine relies on the calories in the fuel that it combusts. Just as different foods have different calorie densities, different fuels also have different calories. A bowl of popcorn has a lot less calories than that same bowl filled with pasta. A gallon of methanol has about half the energy of a gallon of gasoline. A gallon of nitromethane has only about a quarter of the energy of a gallon of gasoline. Our body and our engine use a form of energy conversion to convert the chemical energy stored in the bonds of the food or fuel into mechanical energy that allows us to get from point A to point B.
So how does energy density impact performance? Foods and fuels with high energy density give you more energy per meal or per tankful. If you tried to run a marathon after only consuming a bowl of popcorn the day before, you wouldn’t get too far on the calories provided by that food. Run that same marathon the day after consuming a bowl of high-calorie pasta and the calories from the pasta will take you a lot further. The same holds true for fuels. The energy stored in a tankful of methanol will only take you half as far as the same tank filled with gasoline. Chart A shows the energy densities of some popular fuels and the relative vehicle ranges achievable with a tankful of each fuel.
In addition to the range of the vehicle, the energy density of a fuel will impact the amount of fuel needed to produce a certain amount of power. With gasoline, you need to supply the fuel at a rate of roughly 5cc/min for every horsepower produced at the flywheel. This number is at its lowest when the engine is operating at peak torque and lower elsewhere. To make 1,000 horsepower at the flywheel, about 5,000cc/min of gasoline will be burned (Note: this number is less than the total flow rate of the injectors as injectors need to operate below 85 percent duty cycle, so 1,000bhp is better achieved with 6,000cc/min or 7,000cc/min if 1,000whp is the goal). Switching to a fuel with a lower energy density like E85 ups the amount of fuel required per horsepower. E85 requires about 6.7cc/min for every horsepower produced. To produce 1,000bhp on E85, an engine will consume about 6,800 cc/min of fuel flow (an increase of about 36 percent). Switch to methanol and the injector requirements go even higher. Methanol has only about 51 percent of the energy density of gasoline, so 10.4cc/min of methanol must be burned to produce one horsepower. For a 1,000bhp engine running on ethanol, fuel will be consumed at the rate of 10,400cc/min. Injector sizing and fuel pump delivery demands will be addressed more in the fuel system requirements section. The takeaway should be that energy density will impact vehicle range and the amount of fuel needed to produce a given amount of horsepower. While other fuel options offer significant advantages over gasoline in many areas, gasoline remains one of the highest energy density fuels available. This is one reason why it remains the primary fuel used by spark-ignited engines across the world.
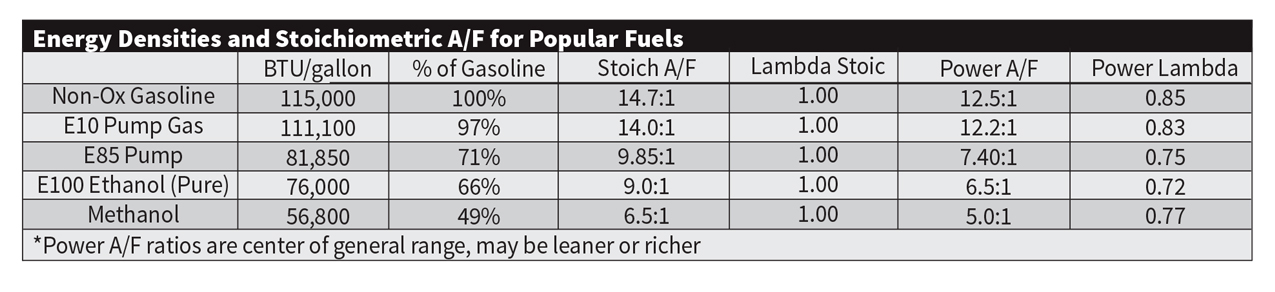
Knock Resistance: Octane Rating
Everyone is familiar with the word octane, even though very few have a complete understanding. Go to any gas station and, in most cases, there are three “grades” of gasoline each with a different octane rating. In California, we have an option between regular grade 87-octane, mid-grade 89-octane and premium-grade 91-octane. In other states, premium fuel octane rating may be as high at 93. As consumers and car owners, there are two facts about octane that just about everyone knows. The higher-priced gasoline grades at the pump are higher in octane and some cars will specify a minimum octane rating or gasoline grade for the vehicle (i.e. Premium Fuel Only). So what is this magic “octane” number all about? The octane rating is simply an indication of how well a particular blend of fuel performs in a laboratory test for knock resistance.
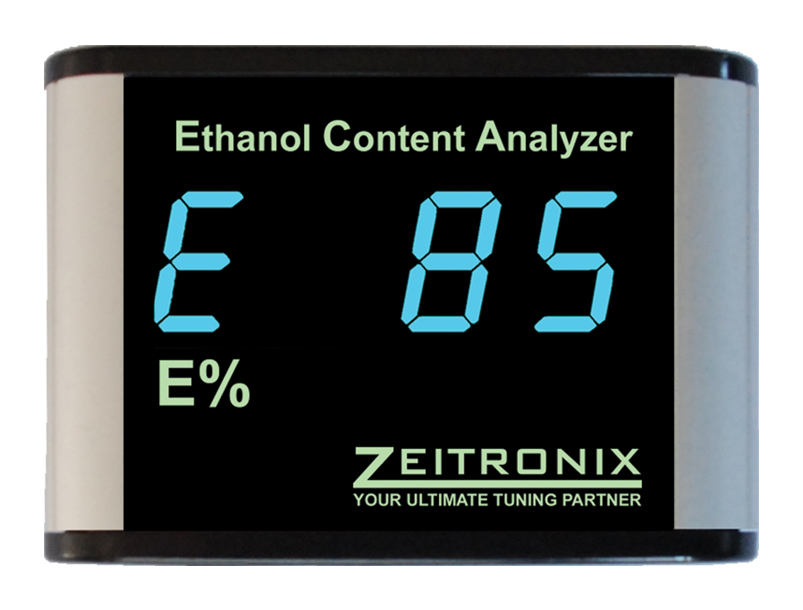
There are two standardized procedures for determining a fuel’s octane number. The Research Octane Number (RON) test conforms to ASTM D2699-19 procedure. The Motor Octane Number (MON) test uses the ASTM D2700-19 procedure. In both cases, an octane number between 0 and 120 is rendered for the fuel. These tests use a 612cc single cylinder engine that can change its compression ratio between 4:1 and 18:1. The compression ratio where the threshold knock level is reached establishes the octane number. The RON test is designed to replicate a constant speed low stress condition. Intake air temperatures are set to 52 degrees centigrade (125.6F) while engine speed is set at 600 RPM with ignition timing at 13 degrees BTDC. Since this is a lower stress test than the MON test, most fuels exhibit a higher RON rating than MON rating. The MON test uses the same engine, but the intake air temp is lowered to 38 degrees centigrade (100.4F) while the engine speed is increased to 900 RPM. Ignition timing for the MON test is varied between 19 and 26 degrees BTDC. The MON test is designed to replicate a heavy load condition for the engine. Hence, a fuel’s MON rating is less than the RON rating. The octane number at the pump is an average of the RON and MON rating. You may have seen the R+M/2 designation when these average octane values are presented at the pump and now you know what it means.
If you followed along, you should be able to deduce that octane requirements increase with an increase in compression ratio when all other factors are equal. All other factors being equal must be stressed as not all engines with a static compression ratio of 10:1 have the same octane requirements. Block material, head material, combustion chamber design, fuel injection technology (port or direct) and cam timing will all play a factor in establishing the minimum octane requirements of an engine to avoid knock. Today’s gasoline direct-injection engines often run compression ratios one to two full points higher than similar port-injection engines. Forced-induction engines (turbocharged and supercharged) have higher octane requirements for a number of reasons. First intake air compression increases the temperature of the charge air. Even effective aftercooling results in higher intake air temps which are more susceptible to knock. Second, the forcing of additional air and fuel into the cylinder increases the engine’s effective compression ratio. Depending on the engine and the modification made, the need for higher octane simply boils down to one question, “do you need more octane to avoid knock”?
Rule number one is never use a fuel of a lower octane value than specified by the car manufacturer. Where this can result in engine damage in earlier vehicles, most modern vehicles will simply suffer a drop in fuel economy and performance.
If you have a non-boosted engine running a factory ECU and tune, increasing the octane rating of the fuel will deliver slight benefits at best. If the factory ECU is adaptive, ignition timing tables may be able to be optimized with a higher-octane fuel. If the factory ECU can only pull timing and not advance and it hadn’t been seeing knock and pulling timing, you won’t see any benefit at all. If you have increased the compression ratio of a non-boosted engine, you will need a higher-octane fuel to avoid knock.
For the forced-induction crowd, the answer to “will your engine benefit from higher octane,” is probably yes for 95-percent of the applications. Even if you don’t raise the boost over factory levels, advanced ignition timing (only achievable without knock when higher octane fuel is used) will result in more power and torque. Case in point, the Mazda3 Turbo vehicle that we just evaluated even specified different power outputs based on the octane rating of the gasoline used. We tested an octane booster on the dyno with this vehicle and proved that it could increase its performance when the fuel’s octane (knock resistance) increased.
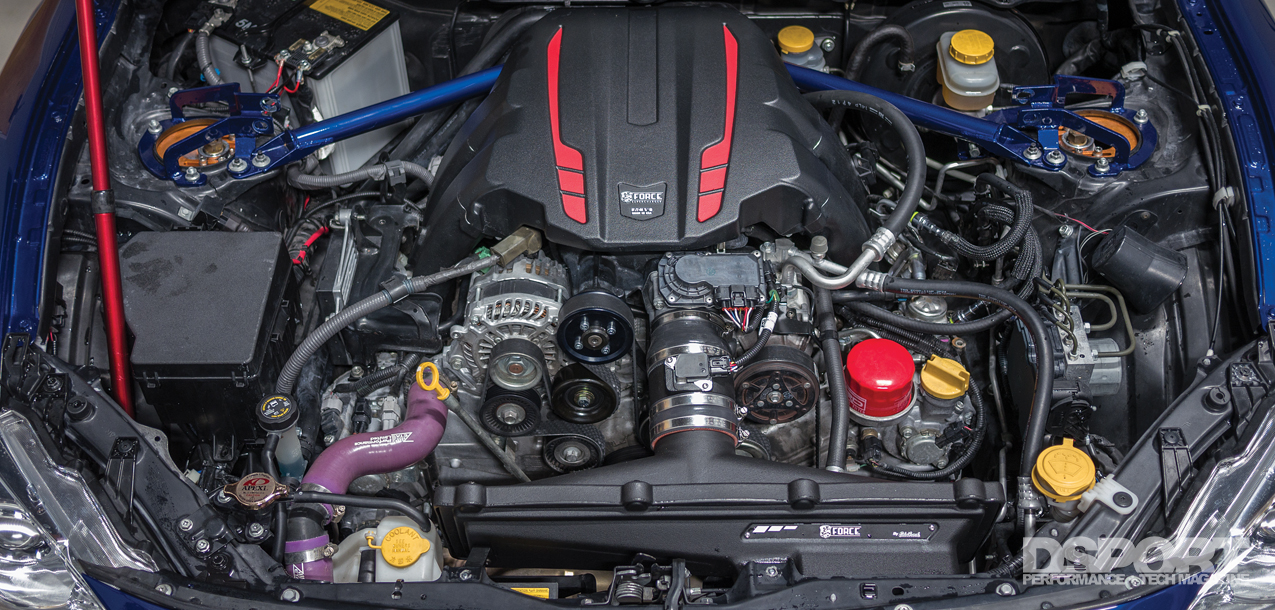
Air/Fuel Ratio
If you remember anything from your high school chemistry class, you may remember how to balance a chemical equation. In the case of combustion of a fuel, a certain number of oxygen atoms from the air need to be combined with a certain number of atoms of the fuel to balance the equation. The perfect balance where all of the reactants (air and fuel) are combusted into the products (carbon dioxide, water, etc.) is called stoichiometric. With non-oxygenation (E0) gasoline, the stoichiometric air/fuel ratio is 14.7 parts of air to one part of fuel (gasoline). So you would need to supply 14.7 grams of air to combust one gram of fuel. Of course, the ideal air/fuel ratio varies depending on the goal (max economy to burn the highest percentage of fuel or maximum power to burn the highest mass of fuel). Ratios where there are more than 14.7 parts of air for every one part of fuel are considered fuel lean or lean for short. Ratios where there are less than 14.7 parts of air for every part of fuel are considered fuel rich or rich for short. Regardless of the fuel used, where it will need to be run richer or leaner in the fuel calibration stays basically the same. Since it is becoming more and more common for a high-performance vehicle to be tuned to run on a different fuel, some tuners are making the conversion to represent air/fuel ratios in terms of lambda. A lambda reading of 1.00 represents a stoichiometric air/fuel ratio, for gasoline it would be equivalent to 14.7:1. A lambda reading of 0.80 represents an air/fuel ratio where there is only 80 parts of air supplied for every 100 parts of fuel (for gasoline that would be an equivalent air/fuel ratio of 11.76:1). It’s important to remember that most air/fuel ratio monitors are not showing the actual air/fuel ratio on the display. They are really showing the lambda value multiplied by the gasoline equivalent of 14.7:1 air/fuel ratio in most cases (unless there are settings to change this value for different fuels).
Different fuels have different stoichiometric air/fuel ratios. E10 gasoline sold at the pump has a stoichiometric air/fuel ratio of 14.0:1 while pure E100 would have an air/fuel ratio of 9.0:1. E85 has a stoichiometric air/fuel ratio of 9.85:1. Methanol comes in at a stoichiometric air/fuel ratio of 6.5:1 while “top fuel,” a mixture of 90 percent nitromethane and 10 percent methanol, has a stoichiometric air/fuel ratio of 2.05:1. So how does a change in this stoichiometric air/fuel ratio with different fuels affect performance? There is going to be a good deal more fuel entering the engine with E85 or methanol versus racing gas. To achieve the same air/fuel ratios, you will require 42-percent more E85 than E10. With methanol, you will be adding 115-percent more fuel to achieve the same air/fuel ratios as E10. This has both positive and negative effects. On the positive side, a higher mass of fuel will pull more heat from the engine as the droplets of fuel are turned from liquid to vapor. On vehicles running high boost levels with marginal intercooling, the additional cooling effect from the additional mass of fuel can drastically reduce the likelihood of preignition/detonation events. This benefit does come with some drawbacks. Since a higher mass of fuel needs to be vaporized, an engine that is cold may have issues with starting. This is the reason that “flex-fuel” E85 in some states that have a winter is changed from an ethanol content of 85 percent to as low as 45 percent. Starting an engine running on methanol on a cold day is even more challenging. Fuel puddling is also much more likely using a fuel like methanol where twice the amount of fuel is being injected into the ports. This is, of course, a nonissue on direct injection engines. Another consideration when using a fuel that has a stoichiometric air/fuel ratio less than gasoline is that airflow can be impacted as fuel is occupying some of the space that would normally be available for the air. Port volumes may need to be slightly increased in some applications to compensate.
Total Energy of Combustion
When you factor the energy density of the fuel with the additional mass of fuel required to balance the chemical equation for combustion, you can get an idea of how much energy can be released for each gram of air that is ingested into the engine. So how much power can be achieved based on increasing this value? If we have an engine running on a non-oxygenated gasoline that makes 1,000 horsepower, an optimized tune for E10 blend will increase the total energy of combustion enough to make 1,022 horsepower realized. Optimizing for E85 raises this number to 1,063, while tuning with methanol bumps the number to 1,121whp. All these numbers are assuming that the knock resistance of the fuel being used is high enough and that the combustion efficiency isn’t being affected. How much does switching to a “top fuel” blend deliver? Horsepower more than doubles to 2,045whp.
While we have shown substantially higher gains than listed above when we’ve gone from pump gas (E10) to E85, these higher gains were not just the gains from the total energy of combustion. These gains were often the result of being able to advance ignition timing and/or increase boost levels thanks to an increased knock resistance and superior cooling effect of the new fuel.
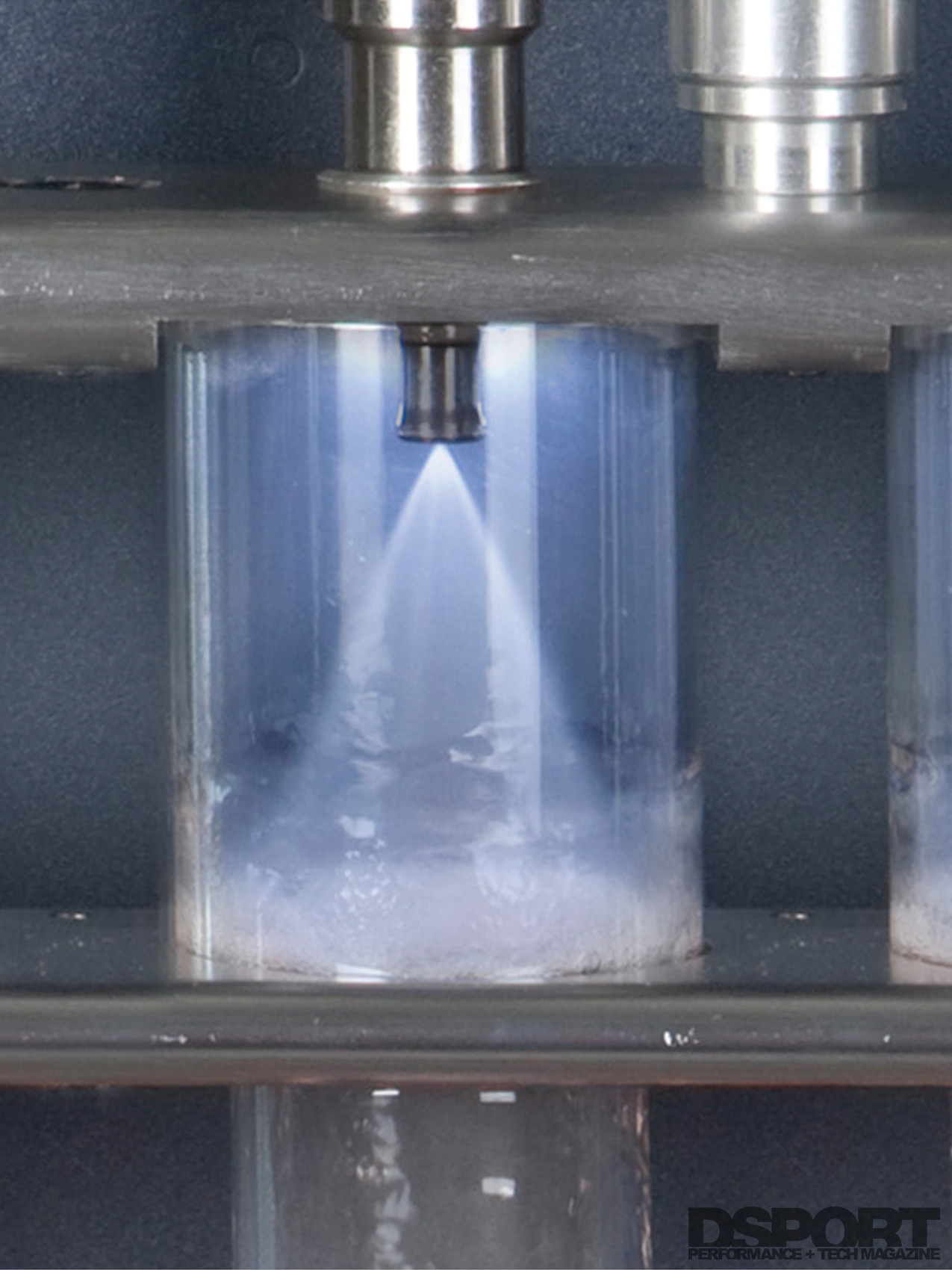
Cooling Factor
If you have ever put an alcohol-based astringent on your face, you are already familiar with the cooling effect that alcohol has. Both ethanol and methanol are alcohols that will pull a significant amount of heat from a surface during vaporization. Whereas it only takes 227 calories of heat used to vaporize a gallon of gasoline, a gallon of E85 requires 2.4 times that amount of heat or 544 calories. With a gallon of methanol, the cooling effect is 3.9 times or 842 calories. While that may already sound impressive, there is an even a higher effective cooling benefit since both E85 and methanol run at richer air/fuel mixtures. When you include the fact that you will be supplying 1.4 times the mass of E85 or 2.0 times the mass of methanol, the cooling effect from E85 is 4.3 times that of gasoline while methanol’s cooling effect is 8.4 times that of gasoline.
In addition to pulling heat out of the intake charge, both ethanol and methanol have a much higher autoignition temperature compared to gasoline. The autoignition temperature of gasoline is just under 500 degrees F while E85 is just under 750 degrees. Methanol is just under 870 degrees. This makes both E85 and methanol extremely difficult to preignite. As a result, both fuels really excel in applications where intake air temperatures are high. Boosted applications with no or minimal intercooling can really excel.
Chemical Considerations
Oxygen content, affinity for water and toxicity are a few of the important considerations when selecting the ideal fuel. The simplest hydrocarbon is methane or CH4. When methane undergoes combustion, all of the oxygen molecules must come from the surrounding as this is a non-oxygenated compound. Other fuels, especially those with alcohol-based compounds, will carry some oxygen atoms along with the hydrocarbon atoms. These fall into a category of oxygenated fuels. Gasoline purchased at the pump averages about 3.5 percent oxygen by weight. E85 is almost 35 percent oxygen by weight while methanol is nearly 50 percent oxygen by weight. The high oxygen content in fuels can be a factor in accelerating wear and corrosion in the fuel system. Alcohol fuels are also hygroscopic, meaning that moisture in the air can make its way into the fuel. This again can lead to accelerated corrosion as acids can form in the fuel when water is present. While ethanol is non-toxic, the same cannot be said for methanol. While methanol may seem like an ideal racing fuel at first glance, we rarely select it as our fuel for a number of reasons that will be discussed in detail in part two.
The Bottom Line
We now have the basic foundation in place to take a look at what the pump and the racing fuel manufacturers has to offer. In part two, we will look not only at the specs on these fuel offerings, but we will also take a look at some example performance combinations better suited for one category of fuels over another. Stay tuned.
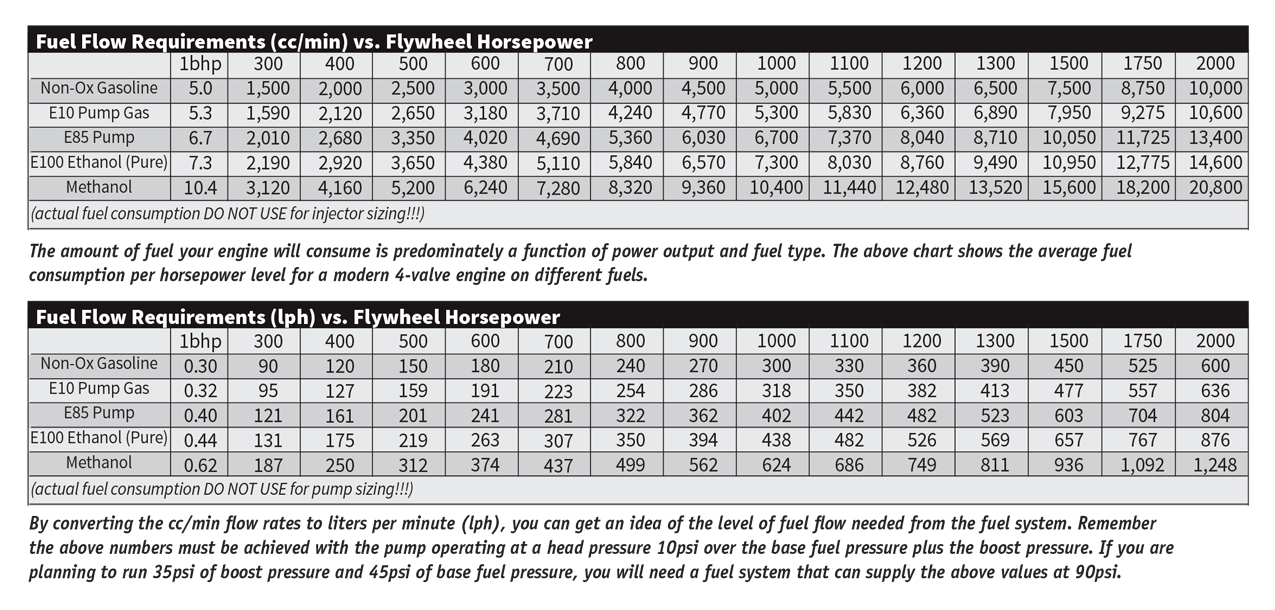
