DSPORT Issue #241
By Michael Ferrara
About a dozen years ago, DSPORT published Allan Lockheed’s Learning Curves article in the June 2010 edition. This article was created to raise the awareness of the importance of the shape of dyno graphs, during a time where everyone was fixated solely on peak horsepower and peak torque numbers (a problem that persists today). For years, this article has served a reference for experienced tuners interested in extracting maximum performance from the engine and vehicle. While all the information and insights provided by Allan in the original article remain facts to this day, advancements in engine control systems have allowed tuners of turbocharged engines to produce specialized curves for specific purposes. These curves include the constant torque and constant power curves achieved by manipulating boost pressure versus engine speed. Before we get into which curve is best for your application, let’s get a proper idea of what torque and horsepower represent.
Torque
We all live in a world that quotes horsepower. However, talking about horsepower before talking about torque is equivalent to putting on your shoes before your socks. Why? Horsepower calculations require knowing both torque output and engine speed (RPM) to calculate horsepower. So let’s start with torque before discussing horsepower. Whether it is realized or not, high-performance enthusiasts have a love-hate relationship with torque. Enthusiasts love what increased torque does in terms of accelerating a vehicle and then they hate what increased torque does in terms of increasing internal engine stresses and decimating clutches, transmissions and axles. Managing torque output from the engine is key to maximizing performance. Before we get into the tuning strategies to manage torque output, let’s first get an understanding of what factors influence torque production.
An engine’s torque output is simply a function of two factors: 1) the engine’s displacement and 2) the engine’s mean effective pressure (MEP). To get more torque from an engine, one must either increase the engine’s displacement or increase the engine’s mean effective pressure. The relationship between torque and displacement are essentially one to one. If you double the displacement of an engine, you would have double the amount of torque output all other factors being equal. The old adage “There’s no replacement for displacement” is proven false with respect to an engine’s torque output as mean effective pressure plays an equally important role in determining torque output. The mean effective pressure represents the theoretical value of a constant pressure that would be applied to the piston during the power stroke to produce the actual amount of work developed during a complete 4-stroke cycle. Whereas, displacement is a constant once the engine is built, the engine’s mean effective pressure (MEP) can vary based on a number of a variables. If modifications and calibrations are done in such a way that the MEP of the engine doubles, torque output will also double.
Torque = ƒ x r
Engine Torque = Displacement x Mean Effective Pressure
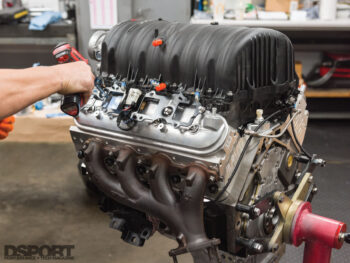
Engine Displacement(The Constant)
An engine’s displacement can only be changed when the engine is being overhauled or “built.” Once the engine is assembled, the displacement is fixed at that constant value until it is torn down, modified and reassembled. This is because displacement is governed by just three factors: cylinder bore area, stroke length and the number of cylinders in the engine. The displacement of a single cylinder in an engine is simply the swept volume of the cylinder. The swept volume is computed by taking the area of the cylinder bore and multiplying by the length of the stroke. If we have a cylinder with an 86mm bore diameter. The radius of the cylinder is one half the diameter or 43mm (4.3cm). To compute the area of this circle, we use the Pi-R-Squared equation and get 3.1415926 * (4.3cm)*(4.3cm). This is equal to an area of 58.09 square centimeters. If the stroke is 86mm also, you can multiple the stroke in cm (8.6cm) times the area in square centimeters (58.09) to get 499.6 cubic centimeters (abreviated as “cc”). A 4-cylinder engine with 86mm bore and 86mm stroke (Nissan SR20 for example) will have a total displacement of 499.6 x 4 = 1,998.3cc. A 6-cylinder with the same cylinder size (Toyota 2JZ) would be 6×499.6 or 2,997.4cc. Since, everyone is more familiar with ft-lb as the unit of torque, it is sometimes helpful to convert from the metric cubic centimeters to cubic inches for later calculations.
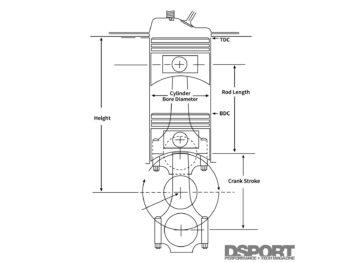
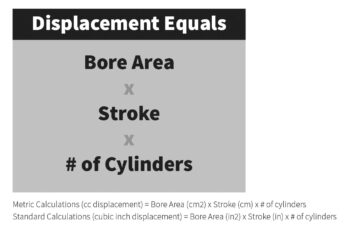
Displacement Units
1,000cc = 61.0237 in3
1.0 Liter = 61 Cubic Inches
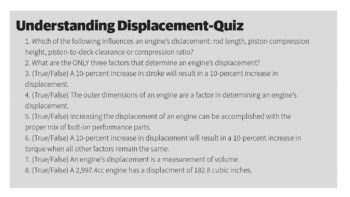
Mean Effective Pressure (The Variable)
While the displacement on an engine is fixed, the mean effective pressure can be varied. If this wasn’t the case, we would be stuck with engines that have a constant torque output which would be tricky to use. Fortunately, there are many factors that influence the mean effective cylinder pressure within the engine. The most obvious torque output control device on an internal-combustion engine is the throttle. Whether direct or drive-by-wire, the throttle acts as the primary regulator of the torque output from the engine. When the throttle is closed or nearly closed, only a small amount of air is allowed into the engine. Under these conditions, only small amounts of fuel can combust and the mean effective pressures are minimal. This is the primary way the torque output of the engine is varied or controlled. When the throttle is wide open (floored), an engine will maximize its torque output. This is how the engine is raced or dyno tested for peak output.
The amount of mean effective pressure achieved is predominately a function of the mass of fuel that can be combusted. The limiting factor for the amount of fuel mass that can be combusted (assuming the fuel supply and delivery system is up to spec) is the mass of air that can be crammed into the cylinders. On a non-forced induction engine, the amount of mean cylinder pressure that can be obtained will be primarily determined by how well the cylinders can be filled. A cylinder that can only be filled with half the mass of air and fuel will only create half the amount of mean effective pressure. The term that relates cylinder filling effectiveness is volumetric efficiency or VE. For a given displacement and engine speed, the VE of an engine is dictated by how well the intake manifold, cylinder heads, camshafts, valves and exhaust manifold can fill the cylinder with a mass of fresh air and the proper measure of fuel. Cylinder head porting, well designed intake manifolds and high-performance camshafts along with eliminating any restrictions in the intake and exhaust tracts are the common ways to increase the VE of an engine. The VE of an engine will also vary with engine speed. The VE will generally gain with engine speed up until the RPM where peak torque is produced. At engine speeds higher than the RPM where peak torque is produced the VE will fall off with engine speed.
While not as large a contributor to mean effective pressure as volumetric efficiency, the thermal efficiency or TE of an engine will also have an impact. The mean effective pressure will also be higher in an engine when the thermal efficiency or TE can be increased. Higher compression ratios, direct injection fuel and optimized ignition and fuel timing calibrations can all help improve the thermal efficiency of the engine. Be careful when choosing to increase the static compression ratio. Although raising the static compression ratio of an engine can raise its thermal efficiency, it can significantly impart the engines volumetric efficiency. Additionally, fuel knock resistance (octane rating) requirements will increase with increases in compression ratio. At the end of the day, the modifications and calibrations that increase an engine’s thermal efficiency are the result of turning more of the energy in the fuel into cylinder pressure to drive the crankshaft at the proper time for maximum torque output.
In addition to volumetric efficiency and thermal efficiency, an engine’s mechanical efficiency will also impact the mean effective pressures. An engine’s mechanical efficiency describes how well it is designed to transfer the up-down motion occuring with the pistons in the cylinders to the rotating of the crankshaft. In general, the older the engine design, the worse its mechanical efficiency. Older engine’s relied upon weaker materials requiring more massive components with wider contact patches to distribute loads. Unfortunately, bigger isn’t always better. The additional contact areas result in higher power losses to friction while heavier pistons, rods and valvetrain require more energy input to get motivated. Often overlooked, optimizing an engine’s mechanical efficiency through the use of narrower rings, narrower bearings, longer rod ratios, optimized valve spring pressures, friction reducing metal treatments and optimized cylinder offset will result in higher mean effective pressures.
Specific Torque Output
The specific torque output of an engine is the amount of torque from an engine for a given displacement. If you haven’t guessed it already, it’s simply another way to discuss the MEP. Honda’s F20C engine produced 77.5lb-ft of torque per liter and that is representative of a good 4-valve, variable cam timing, port injection running on pump gas engine. In comparison, the best Pro Stock, NASCAR and Formula One engines generate in the neighborhood of 90-95lb-ft of torque per liter.
Specific Torque Output
65 lb/ft per liter General Performance OEM
70 lb/ft per liter Mid-Performance OEM
75 lb-ft per liter High-Performance OEM
77.5 lb-ft per liter Honda F20C
80 lb-ft per liter Well-Developed Street/Strip
85 lb-ft per liter Well-Developed Racing
90-95 lb-ft per liter F1, NASCAR, Pro Stock
Boost Your Pressure Ratio
So how does forced induction affect mean effective pressure? Forced induction increases the mass of air and fuel compacted into the cylinders. The result is higher mean effective pressures in the engine. Depending on the amount of power taken from the engine to drive the compressor in the forced induction system, you will see as much as double the amount of torque for a doubling of the pressure ratio (boost pressure is equal to 14.5psi). At 29psi, you could get up to three times the MEP and torque output. At 43.5psi, the pressure ratio is 4 times atmospheric and the highest potential torque increase is also 4-fold. These possibilities assume that the compressor(s), charge-air coolers and the compressor driver are all working in an efficient operating range.
Torque=Cylinder Pressure
While torque output is directly proportional to a theoretical value termed the mean effective pressure, its also directly proportional to actual in-cylinder pressure during combustion. If you double the torque of an engine at a certain engine speed, you’ve also doubled the average cylinder pressures during the power stroke. When these cylinder pressures are within the range that the head gasket and head fasteners can handle, there isn’t really an issue. When cylinder pressures go beyond these limits, the combustion seal is compromised and a head gasket failure occurs.
Because of the relationship between torque and cylinder pressure, we often will regulate boost to set a constant torque value that is slowly increased during the engine development and tuning process. This is a great way to extract maximum power with minimal engine stress. Making 600 horspower at 5,252RPM requires 600lb-ft of torque and the cylinder pressures required to make the engine get there. Take that same engine to 7,000RPM to make 600 horspower and the torque only needs to be 450lb-ft. That’s 25-percent less cylinder pressure.
Horsepower Defined
Torque and horsepower are directly tied together by engine speed (RPM). If you know the torque output and engine speed (RPM), you can compute the horsepower. If you know the horsepower and engine speed (RPM), you can compute the torque. The equations are as follows:
Horsepower = Torque (lb/ft) * Engine Speed (RPM) / 5,252
Torque (lb/ft) = Horsepower * 5,252 / Engine Speed (RPM)
If we have two engines at the same engine speed (RPM) and one engine is making twice the torque of the other engine, it will also be making twice the horsepower at that engine speed.
A great analogy is to think of torque and engine speed (RPM) as the punching force (torque) and punching frequency (engine speed/RPM) of a character in a fighting game. A high-horsepower character would be able to deliver the most damage in a set amount of time. Let’s say a full second of attacks from two different characters could both defeat the same boss. This would mean both of these characters have the same horsepower. One might be a character with a very strong punch (high torque) that only unloads twice per second (low RPM), while the other character with the same horsepower might deliver a strike that only does 20-percent of the damage of the other. In this case, the second character would need to deliver five times as many hits in the same period to have the same horsepower of the other character.
As an engine spins faster, it delivers more combustion events for a given amount of time. At 600RPM, an engine makes 10 revolutions per second. In 10 revolutions, every cylinder has been fired five times. At 6,000RPM, an engine is having every one of its cylinders firing 50 times per second. At 12,000RPM, every cylinder fires 100 times per second. Even if an engine at 12,000RPM is only making half the torque of a different engine at 3,000RPM, it will still be making twice the power. It will have 100 strikes at half power versus only 25 strikes at full power.